Are you struggling to replace a thermocouple on your gas water heater? Don’t worry, we’ve got you covered.
In this guide, we’ll walk you through the simple steps to replace the thermocouple and other vital elements. Plus, we’ll show you how to test everything to ensure your water heater runs smoothly.
Let’s get started!
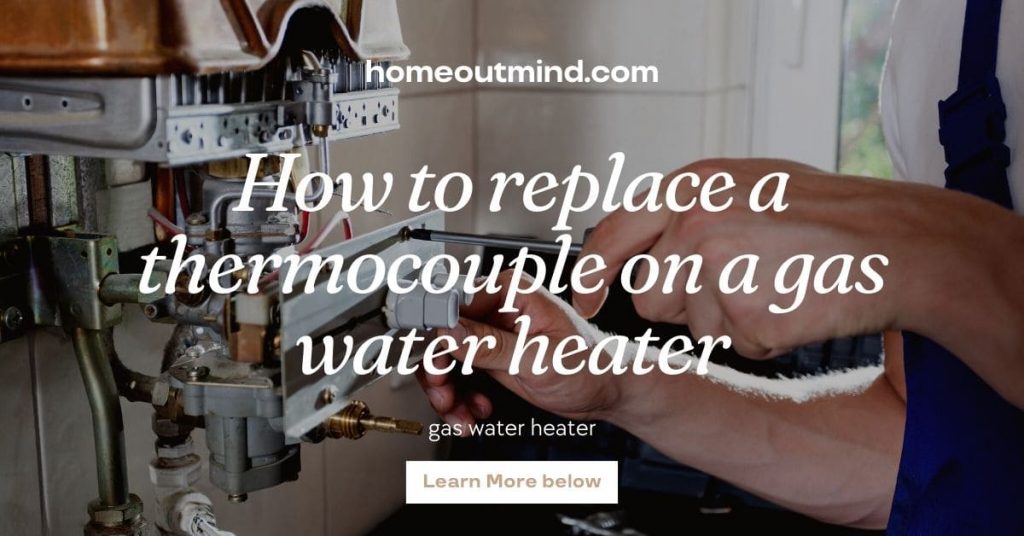
What is a gas water heater thermocouple?
Before we dive into the replacement process, let’s take a moment to understand what a thermocouple is and why it’s essential for your gas water heater.
A thermocouple is a sensor that detects the presence of a pilot flame. If the pilot flame goes out, the thermocouple shuts off the gas supply to prevent a dangerous gas buildup.
Over time, thermocouples can wear out or become faulty, leading to issues with your water heater’s performance.
How to Replace a thermocouple on a gas water heater in 10 steps
Step 1. Testing Your Thermocouple
Before replacing your thermocouple, it’s essential to confirm that it’s the culprit behind your water heater issues. We’ll walk you through two common testing methods: closed circuit testing and open circuit testing.
With a multimeter and some basic tools, you can determine whether your thermocouple needs replacement or if the issue lies elsewhere in your water heater system.
Step 2: Turn Off the Gas Supply
Safety first! Locate the gas shut-off valve on your water heater and turn it to the “OFF” position.
This will ensure that no gas is flowing to the appliance while you work on it, minimizing the risk of accidents.
Step 3: Remove the Outer Jacket Door
Using a screwdriver or the appropriate tool, carefully remove the outer jacket door of your water heater. Set it aside in a safe place where it won’t get damaged or misplaced.
Step 4: Disconnect the Thermocouple
Next, locate the thermocouple attached to the gas valve. Depending on your water heater model, it may be secured with a nut or screw.
Use the appropriate tool to loosen and remove the fastening mechanism, then gently disconnect the thermocouple from the gas valve.
Step 5: Remove the Old Thermocouple
Once the thermocouple is disconnected, carefully remove it from its mounting bracket near the pilot light.
Take note of how it’s positioned and any clips or brackets holding it in place.
Step 6: Install the New Thermocouple
Now, it’s time to install the new thermocouple. Position it in the same location and orientation as the old one, ensuring that it’s securely seated in the mounting bracket.
If necessary, use clips or brackets to hold it firmly in place.
Step 7: Reconnect the Thermocouple
With the new thermocouple in place, reconnect it to the gas valve using the fastening mechanism you removed earlier.
Make sure the connection is snug and secure to prevent any gas leaks once the water heater is back in operation.
Step 8: Replace the Outer Jacket Door
Once the thermocouple is securely installed and connected, replace the outer jacket door of your water heater.
Use your screwdriver or tool to reattach any screws or fasteners, ensuring that the door is properly aligned and sealed.
Step 9: Turn On the Gas Supply
With the replacement process complete and everything securely in place, it’s time to turn the gas supply back on.
Locate the gas shut-off valve and switch it to the “ON” position, allowing gas to flow to the water heater once again.
Step 10: Test the Water Heater
Before calling it a job well done, it’s essential to test your water heater to ensure that everything is functioning correctly.
Follow the manufacturer’s instructions for relighting the pilot light and operating the water heater. Keep an eye out for any unusual sounds or smells, which could indicate a problem that needs further attention.
Are There Signs That Indicate My Thermocouple Needs Replacement?
Yes, there are several telltale signs that your thermocouple may need replacement. One common indication is if the pilot light on your gas water heater frequently goes out without any apparent reason.
Additionally, if you notice that your water heater isn’t producing hot water consistently or at all, it could be due to a faulty thermocouple.
Another sign to watch for is a weak or irregular pilot flame. If you observe any of these symptoms, it’s likely that your thermocouple needs to be replaced.
What Tools Do I Need to Replace a Thermocouple on a Gas Water Heater?
To replace a thermocouple on a gas water heater, you’ll need a few basic tools. These typically include a screwdriver (both flathead and Phillips), pliers, and possibly an adjustable wrench.
Additionally, you may need a flashlight for better visibility, especially if your water heater is located in a dimly lit area.
Of course, don’t forget to have a replacement thermocouple on hand that is compatible with your specific water heater model.
How Can I Safely Turn Off the Gas Supply to My Water Heater?
Ensuring safety is paramount when working with gas appliances. To safely turn off the gas supply to your water heater:
- Locate the gas shut-off valve, which is usually located on the gas line near the appliance.
- Rotate the valve handle or lever to the “OFF” position to stop the flow of gas.
It’s essential to make sure the valve is fully closed to prevent any gas leaks. Additionally, ensure proper ventilation in the area and avoid using any open flames or electrical appliances while working on your water heater.
Is it Possible to Test a Thermocouple Before Replacing it?
Yes, it is possible to test a thermocouple before deciding to replace it. Using a multimeter set to measure millivolts, you can perform various tests to determine if the thermocouple is functioning correctly.
One common test involves measuring the voltage output of the thermocouple while the pilot light is lit. If the reading falls within the expected range, typically around 25 to 30 millivolts, it indicates that the thermocouple is working properly.
If the reading is significantly lower or nonexistent, it may be time to consider replacing the thermocouple.
What Are Common Mistakes to Avoid When Installing a New Thermocouple?
When installing a new thermocouple on your gas water heater, there are several common mistakes to avoid to ensure a successful replacement.
One mistake is overtightening connections, which can damage threads or cause leaks.
It’s important to tighten connections securely but not excessively. Another mistake is misaligning the thermocouple during installation, which can affect its performance.
Make sure the thermocouple is properly positioned and secured in place according to the manufacturer’s instructions.
Additionally, don’t forget to test the water heater after installation to ensure everything is working correctly and there are no issues with the new thermocouple.
Frequently Asked Questions
How to replace thermocouple on water heater
Replacing a faulty thermocouple is necessary if your water heater’s pilot light won’t stay lit. Start by turning off the gas supply and pilot light.
Remove the old thermocouple from the control valve and install the new one, ensuring it’s securely attached. Relight the pilot light according to manufacturer instructions.
For detailed replacement steps and troubleshooting tips, explore our article on How to Replace a Thermocouple on a Water Heater.
How to fix RV water heater
Fixing an RV water heater involves several steps to ensure proper operation. Start by inspecting the heater for visible signs of damage or malfunction.
Check the burner assembly, ignition system, and connections for any issues. If necessary, clean or replace components as needed. Additionally, check for leaks and address them promptly.
For a comprehensive guide on troubleshooting and fixing RV water heaters, explore our article on How to Fix an RV Water Heater.
How do you turn on an electric water heater
Turning on an electric water heater is a simple process. Locate the circuit breaker or fuse box in your home and ensure the breaker or fuse corresponding to the water heater is in the “on” position.
This step provides power to the water heater’s heating elements. For detailed instructions and safety precautions, refer to our comprehensive guide on How to Turn On an Electric Water Heater.
How to clean tankless water heater
Regular cleaning is essential to maintain the efficiency of a tankless water heater. Start by turning off the power and water supply to the unit.
Remove any debris or mineral buildup from the inlet filter and flush the system with vinegar or a descaling solution to remove scale deposits. Rinse thoroughly and reinstall the filter.
For detailed cleaning instructions and maintenance tips, refer to our comprehensive guide on How to Clean a Tankless Water Heater.
Why is the water heater leaking
Water heater leaks can occur due to various reasons, including loose fittings, corroded pipes, or a faulty pressure relief valve. Inspect the water heater for visible signs of leakage and address any loose connections or damaged components.
If the leak persists, check the pressure relief valve for malfunctions and replace it if necessary. For a detailed explanation of common causes and troubleshooting tips, refer to our article on Why Is the Water Heater Leaking?.
Conclusion
In conclusion, replacing a thermocouple on a gas water heater is a manageable DIY task that can be completed with the right tools and knowledge.
By following the step-by-step guide provided and adhering to safety precautions, you can restore your water heater’s functionality and ensure reliable hot water for your home.
Remember to test the water heater after installation to confirm proper operation, and don’t hesitate to seek professional assistance if needed. With this simple maintenance task, you can enjoy peace of mind knowing that your gas water heater is in good working condition.